20Khz Auto Tracking Ultrasonic Machining Vibration Milling
EequipmentDescription
Frequency: | 20khz | Power: | 1000W |
---|---|---|---|
Amplitude: | 15~50um | Gap Overcut: | 0.02-0.1 |
High Light: | rotary ultrasonic machining,ultrasonic assisted drilling |
20Khz ultrasonic vibration milling transducer for metal cutting
Introduction:
Classical technologies of ultrasonic material processing allow one to obtain surface and subsurface nanostructures, but only auto-resonant technologies can ensure the stability of structuring and obtaining the desired properties of the surface and nanocrystalline structures with certain parameters. Obtaining of specific and highly efficient (in terms of physical and mechanical properties) nanocrystalline structures at auto-resonant ultrasonic cutting steel copper and brass points to the importance of learning and developing of a method of ultrasonic cutting and smoothing of materials. A number of other industrial auto-resonant ultrasonic devices have been elaborated. • Pecialized equipment for surface hardening of work-pieces to improve the surface finish and to harden the surface layer of the material. • Wire drawing device to manufacture such delicate wires as thin filaments of precious metals. • Ultrasonic apparatus for dimensional processing of holes and cavities of arbitrary shape in brittle materials. In parallel with the industrial auto-resonant ultrasonic equipment we also propose household devices. • Putty knife: intended for surface plastering and filling; eliminates putty sticking to the instrument; allows obtaining thin layers of putty; provides its better adhesion to the working surface. A similar device can be used to apply creams with cosmetic and medicinal purposes. • Knife: intended for cutting products prone to crumpling, squashing and sticking (fresh bread, cheese, cakes, etc.). • Chisel: designed for wood carving and channeling in wood products, for example, sockets for mortise locks. • Kreytsmeysel: intended for cutting metal, for example, for engraving on metallic surfaces or making moulds for precious metal jewelry. • Blade sharpening device for knives and scalpels: sharpens blades simultaneously with hardening of the material by plastic deformation (whetting) of the blades. It can be used, for example, for whetting the scythe blades. This list can be greatly extended, first of all, due to various vibration technological machines operating in sub-ultrasound-frequency bands
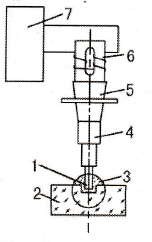
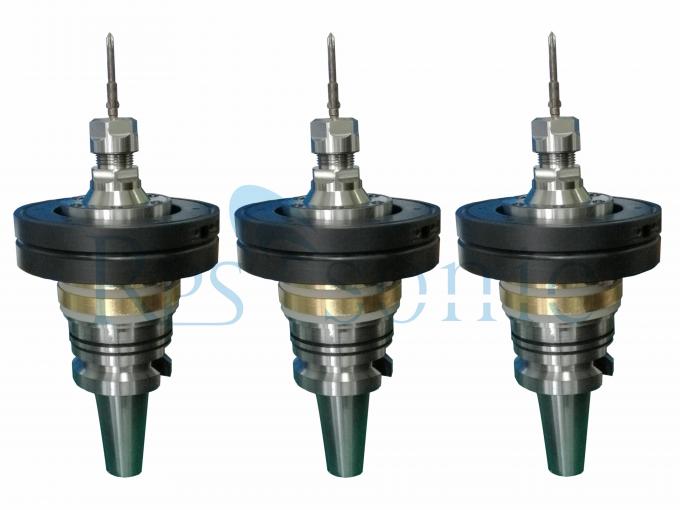