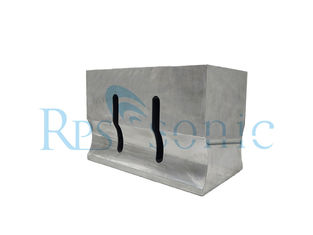
In the world of ultrasonic technology, innovation is a constant driving force. The need for more efficient and effective tools to enhance the capabilities of ultrasonic equipment has led to the development of a wide spray type nozzle for flux spraying. This groundbreaking solution is set to revolutionize the way flux is applied in various industrial processes, thanks to the pioneering work of RPS-SONIC.
RPS-SONIC is a company comprised of a group of young, passionate individuals who have a deep love for ultrasonic technology. The founding members of RPS-SONIC possess at least a Bachelor's degree and have accumulated over 5 years of experience in the ultrasonic industry. Their dedication and expertise have enabled them to push the boundaries of ultrasonic technology and develop innovative solutions that cater to the evolving needs of various industries.
The introduction of the wide spray type nozzle for flux spraying is a testament to RPS-SONIC's commitment to advancing ultrasonic technology. This nozzle is designed to provide a more uniform and efficient application of flux, which is a crucial component in the soldering process of electronic assemblies. The traditional methods of flux spraying often result in uneven coating and wastage of the flux material. However, with the wide spray type nozzle, these issues are effectively addressed, leading to improved soldering quality and reduced material consumption.
The key feature of the wide spray type nozzle is its ability to produce a broad and uniform spray pattern, covering a larger surface area with a consistent layer of flux. This results in better coverage of the solder joints, ensuring a more reliable and stable connection in electronic assemblies. Moreover, the nozzle is designed to minimize overspray and reduce material waste, thereby optimizing the usage of flux and lowering operational costs for businesses.
One of the main advantages of the wide spray type nozzle is its versatility. It can be easily integrated into existing ultrasonic soldering equipment, allowing businesses to upgrade their systems without the need for major investments or overhauls. This seamless compatibility makes it a convenient and cost-effective solution for companies looking to enhance the performance of their soldering processes.
RPS-SONIC's wide spray type nozzle is a product of extensive research and development, backed by the company's deep understanding of ultrasonic technology and its practical applications. The team at RPS-SONIC has leveraged their rich experience in ultrasound to create a nozzle that meets the stringent demands of modern industrial processes. It undergoes rigorous testing to ensure its reliability and performance, providing businesses with a solution that they can trust to deliver consistent and high-quality results.
In addition to its technical capabilities, the wide spray type nozzle is also designed with user-friendliness in mind. It is simple to install and operate, requiring minimal training for personnel to use effectively. This ease of use further contributes to its appeal as a practical and efficient solution for flux spraying in various industrial settings.
The introduction of the wide spray type nozzle for flux spraying marks a significant milestone in the evolution of ultrasonic technology. RPS-SONIC's relentless pursuit of innovation has resulted in a product that is set to elevate the standards of flux application in the soldering process. With its emphasis on precision, efficiency, and cost-effectiveness, the wide spray type nozzle is poised to become an indispensable tool for businesses seeking to optimize their soldering operations.
For companies looking to stay ahead in the competitive landscape of industrial manufacturing, the wide spray type nozzle for flux spraying from RPS-SONIC presents an opportunity to enhance the quality and efficiency of their production processes. With this groundbreaking solution, the future of ultrasonic technology continues to evolve, opening new possibilities for improved performance and productivity in industrial applications.