20Khz ultrasonic dip tinning welding Ultrasonic Solder Pots
ParameterModel No. | RPS-DS20 | |
Ultrasonic Frequency | 20Khz | |
Maximum Output | 1000 Watt | |
Temperature Range | 150 ~ 400 °C | |
Power Supply | 220V / 50-60 Hz | |
Ultrasonic Generator | Size | 250(W) x 310(L) x 135(H) mm |
Weight | 5 Kg | |
Feature | Ultrasonic Amplitude Adjustable | |
Pot dimension | 20*15cm | |
Avail Soldering Matrial | ITO Glass, AL, Mo, Cu etc., |
- Aluminum components
- Ferrite components
- Glass components
- Silicon wafers
- Ceramic components
- Semiconductor chips
- Metals etc.
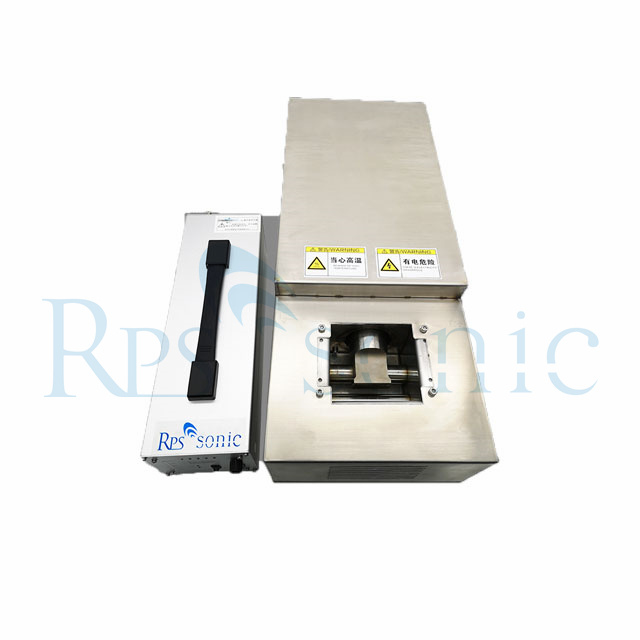
- Easy soldering upon un-bondable material (metal, glass, ceramics) by simple dipping process.
- No need for flux
- Reliable bonding/sealing
- Best used in difficult, small-surface places with limited access
- Ceramic components
- Semiconductor chips
- Metals etc.