20Khz 2000w High Power Ultrasonic Harness Welding Machine
ParameterPower | 2000W | Frequency | 20KHZ |
Power supply | 220V | Gas source | 0.5kg |
Way to control | Single chip microcomputer | Maximum working stroke | 30mm |
Welding area range | 0.3M2-10M2 | Welding time range | 0.2s---5s |
Welding mode | Automic | Quality control | 1year |
Dimensions | 500LX400WX230H MM | Total Weight | 52kg |
Generator size | 400LX290WX130H MM | ||
Features:Automatic tracking of energy, time, welding time, energy, air pressure, width, amplitude adjustable |
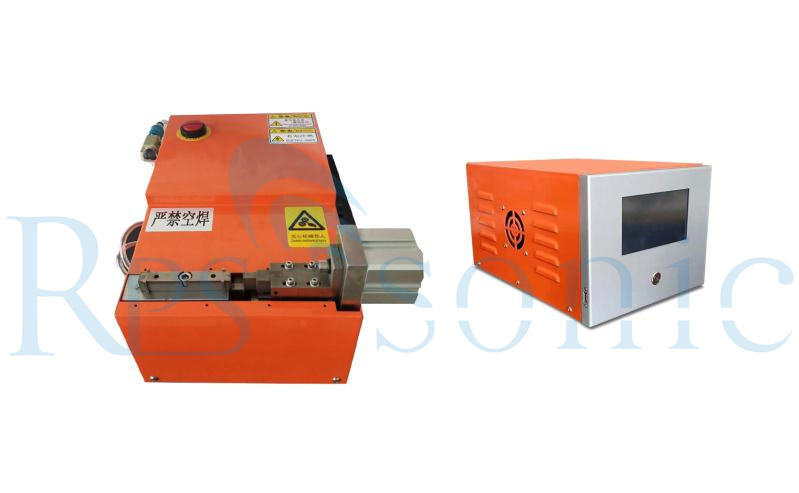